WIPER INSERT
Improving Surface Finish
Under the same machining conditions as conventional breakers, but with the feed rate
increased, the surface finish of the workpiece can be improved.
Improving Efficiency
High feed rates not only shorten machining times but also make it possible to combine
roughing and finishing operations.
Increased Tool Life
When using to high feed conditions, the time required to cut one component is decreased,
thus more parts can be machined with each insert. In addition, the high feed rate prevents
rubbing, therefore, delaying the progression of wear and increasing the tool life of the insert.
Improving Chip Control
Under high feed conditions, the chips generated become thicker and are more easily
broken, thus, chip control is improved.
Insert example
Conventional wiper insert
Wiper insert for low rigidity workpieces
CBN wiper inserts for low rigidity workpieces are now available in MBC010, MBC020 and MB8025 grade, making it suitable for use in
application areas where conventional inserts cannot be used due to vibrations.
CUTTING PERFORMANCE
<Cutting Conditions>
- Workpiece:
- Hardened Material (HRC60)
- Insert:
- NP-CNGA120408
- Cutting Speed:
- 120m/min
- Feed:
- 0.2mm/rev
- Depth of Cut:
- 0.1mm
- Dry Cutting
-
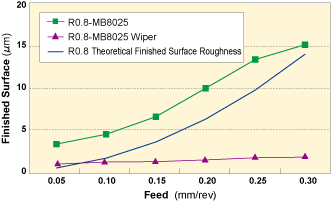
NOTES FOR USE
No Restriction for Holders
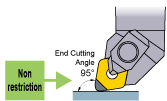
A standard holder can be used.
(*A double clamp, high rigidity tool is recommended.)
Restriction for Holders
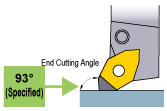
Use a holder with end cutting angle 93° for improving wiper efficiency. A holder with end cutting angle 91° can improve wiper efficiency, however, there is no wiper efficiency with other end cutting angles (60°, 90°,107°etc.).
RECOMMENDED CUTTING CONDITIONS AND PERFORMANCE